How to Apply 5 Whys Root Cause Analysis
The root cause analysis aims to dig deep into a particular problem to identify its primary cause. One of the most significant challenges we face when trying to solve a problem is that what we perceive as the real cause is the effort or the symptoms. It is an outcome effect of one or more root problems. As a result, the solutions we generate will walk in the wrong direction and will not help solve the issue. Moreover, it can make it more worthwhile. Tools like the 5 Whys technique, Cause-Effect diagram, and Failure Mode and Effects Analysis are designed to help us investigate the problem’s primary root cause, which can contribute to finding the right solution.
Previously, we explored other tools like the Failure Mode and Effects Analysis (FMEA) and Cause-Effect Diagram (Ishikawa diagram) that can explore the different causes of complex problems and understand why it occurs by investigating the possible factors that may lead to the final potential root causes throughout problem prevention. However, it may be a time-consuming tool for start-ups that are assumed to need more time and resources. Also, it may be more suitable for complex situations rather than a simple one.
What is the 5 Whys Root-Cause Analysis?
The 5 Whys is another root cause analysis powerful tool that can help the team to investigate the root causes of a problem or number of problems by asking a simple question (why) five times. By repeatedly asking “Why?” and exploring the responses, the method aims to reveal the fundamental cause of a specific problem rather than addressing only its symptoms.
The 5 Whys analysis tool is coined by Sakichi Toyoda, the Japanese inventor and founder of Toyota Industries. He developed the technique back in the 1930s. It was applied in the Toyota production system and is still used today to find the problem’s root cause. The tool is based on counter-measures methodology, which aims to use insights to identify the root causes of the problem and prevent it from happening by recognising the human error behind the observed symptoms. This approach makes it more efficient than the traditional methods that only target solving the outcome effect. This core concept behind the tools makes them practical and lean as they can investigate one or more problems.
- Benefits of Using 5 Whys in Root Cause Analysis
- How to Apply the 5 Whys Tool
- Apply the Root Cause Analysis to Find Solutions
- Using the 5 Whys with the Cause-Effect Diagram
The 5 Whys tool focuses on addressing problems with the following approach considered in mind:
- Precise problem definition: Clearly defining the specific problem at hand.
- Goal setting: Establishing clear objectives to guide the problem-solving process.
- Root cause analysis: Identifying the underlying causes of the problem by repeatedly asking, “Why?”.
- Implementing counter-measures: Developing and implementing practical solutions to address the root cause.
- Monitoring, standards, and follow-up: Establishing checks and measures and conducting regular follow-up activities to ensure the problem remains resolved.
Generally, there are three main types of root-cause analysis procedures:
Logic root-cause analysis is a method used to identify the root causes of a problem by employing logical reasoning and critical thinking. It involves examining the logical connections and relationships between events, actions, or factors to trace back to the fundamental causes.
One-variable-at-a-time (OVAT) root cause analysis, also known as single-factor analysis, is a method used to identify the root cause of a problem by systematically varying and analysing one variable at a time while keeping all other factors constant. This approach is commonly employed in scientific experiments and industrial settings to isolate the impact of individual variables on the outcome or problem being investigated.
Multivariate-at-a-time (MVAT) root cause analysis, also known as multivariable or multivariate analysis, is a method used to identify the root cause of a problem by simultaneously considering and analysing multiple variables or factors. Unlike the one-variable-at-a-time approach, which focuses on isolating individual variables, multivariate analysis allows for examining interactions and relationships among various variables to understand their combined impact on the problem.
The 5 Whys lies under the logical category, which requires no math or statistics experience, making it more flexible and approachable for designers with no statistical background.
Benefits of Using 5 Whys in Root Cause Analysis
Besides identifying the root causes of a problem, there are other advantages of using the 5 Whys method, including the following:
- It can help us to determine the relationship between the origins of a problem as endless questions draw a linkage between different causes during the discussion.
- Its simplicity helps the team learn how to use it quickly and efficiently during meetings. It doesn’t need any statical analysis for problems.
- It is a time-flexible and lean tool that can analyse simple and complex issues.
- It can be used with other tools, such as the cause-effect diagram and Failure Mode and Effects Analysis, to have an accurate outcome, verify the findings, and ensure they are the real root causes.
How to Apply the 5 Whys Tool
Before applying the 5 Whys in root cause analysis, we assemble the team, which usually consists of the stakeholders involved in the problem and represents the different related departments. Then, we assign a facilitator who is expected to manage the discussion among team members. The facilitator’s role is to ensure that the process moves from one step to another with an in-depth analysis of the findings at each stage. Also, the facilitator needs to ensure that the discussion is targeted, the meeting is conducted within the planned timeframe, and that more sessions are required. Applying the 5 Whys tool can follow the below steps:
Step 1: Define the Problem
The facilitator defines and writes down the problem that needs to be investigated and describes it accurately to ensure that all the team members understand it. For example, patients don’t attend their doctor’s appointments.
Step 2: Ask the Why questions
A sequence of around five why questions is formed based on the statement above as follows:
- Patients don’t attend their/miss doctor appointments. Why?
- The appointment message only alerts them after the doctor’s session. Why?
- The messages don’t have an alert feature. Why?
- The system doesn’t allow repeated messages or link appointments to patients’ calendars; why?
- The system doesn’t include an alerting or follow-up feature.
The last sentence is the root cause of the patient missing appointments. The 5 Whys can take further steps until the team feels that they reached the real cause of the problem. The number of questions asked may be less or more than five questions until we reach the root cause of the situation where there are no questions that can be asked (check also What is an Affinity Diagram? And How to use it?).
Step 3: Discussing the results
The 5 Whys can take one route, as shown in the example above, or multiple directions when there is more than one cause. In the case above, the team concluded the root cause after only four why questions. The result is that they need a feature in the system that can alert the patients before their appointment or allow them to add the appointment meant to their calendar.
Multi-Lane 5 Whys Method
When applying the 5 Whys method, we find that sometimes, there is more than one route (answer) for the why question. This may vary depending on the problem and the rationale behind each answer. As shown in the figure below, we develop the multi-lane 5 Whys diagram in this situation.
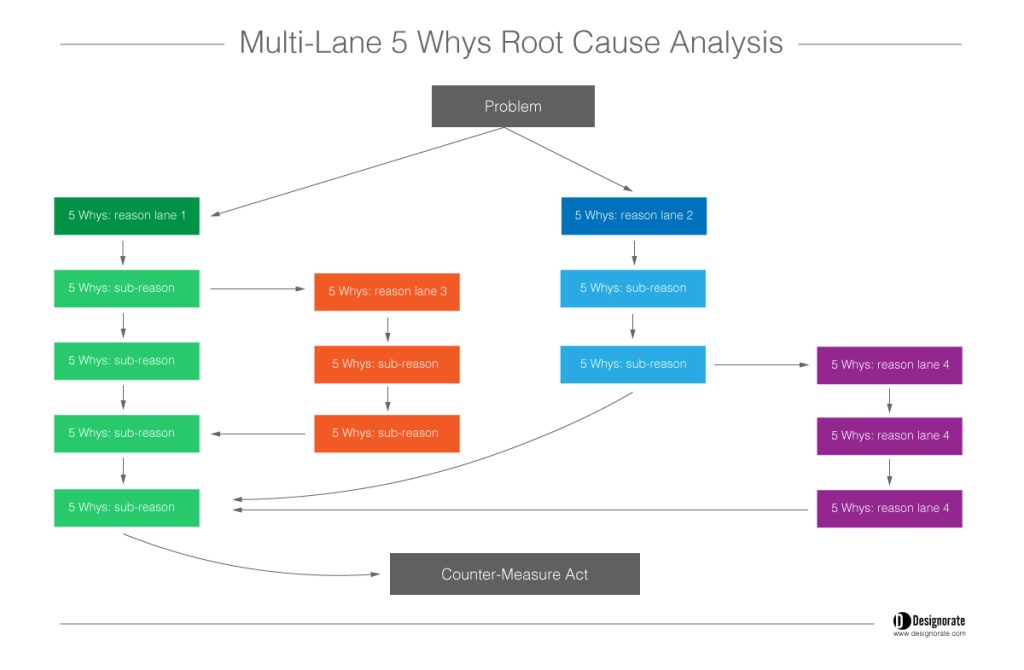
The answer to each question can branch to more than one reason, which generates a second parallel lane of enquiry that can lead to a second sequence of why questions. While the investigation in this route may extend further due to the multiple questions answered, interrogating the situation can lead to one or more root-cause problems to address (How to Use Decision Trees in the Decision-Making Process).
Apply the Root Cause Analysis to Find Solutions
The main aim of using the 5 Whys tool is to identify the root cause nature of the problem. However, they need to investigate the solution to the root cause. Different techniques can be used to solve problems, such as the TRIZ method. Brainstorming (e.g. reversed brainstorming, online brainstorming and Brainstorming Charette Procedure) can be used as a simple tool to discuss the various possible solutions and explore their parts.
Using the 5 Whys During the Design Thinking Process
Double Diamond Design Thinking is a framework that guides the design process by providing a structured approach to problem-solving and innovation. It visually represents the design thinking process, highlighting divergent and convergent thinking stages. During the Double Diamond Design Thinking, we implemented several tools to help us discover problems, such as reversed brainstorming and SCAMPER with a critical thinking mindset. However, we need to identify the problem’s root cause to accurately define it in the Define stage of the design thinking process.
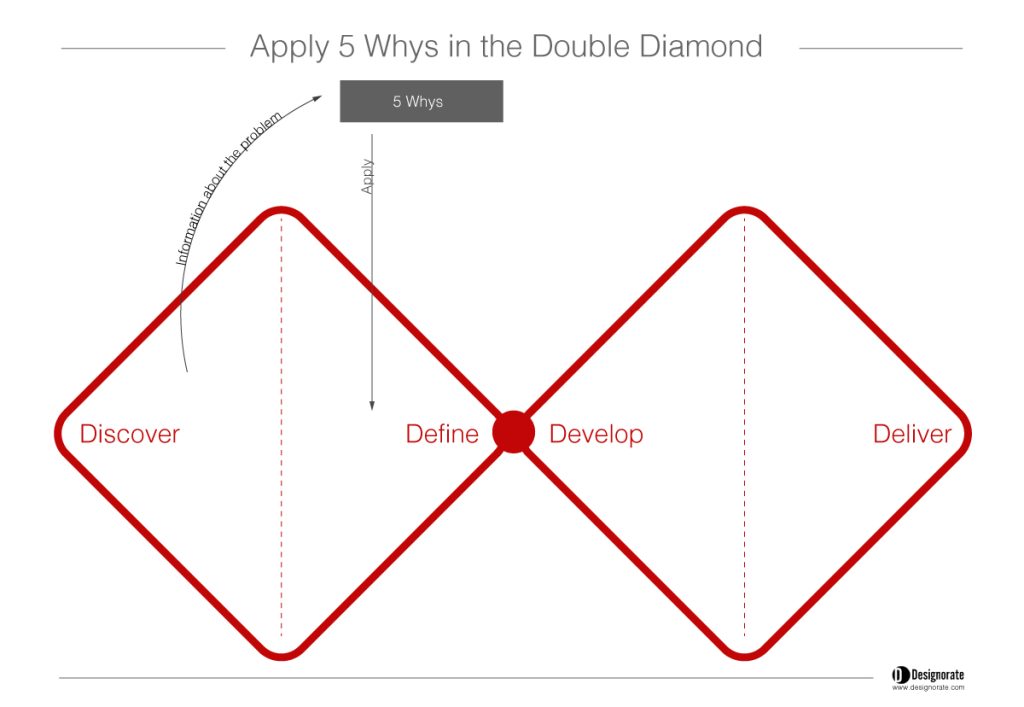
The 5 Whys method can play an essential role during the Define stage. After collecting data about the problem or design challenge in the Discover stage, we can use the 5 Whys tool in the Define stage to identify the root cause of the problem, which we can illustrate in a clear statement to guide the solution space of the design thinking process as shown in the figure above. In addition to the design thinking, 5 Whys can be used in other processes such as the Stage-Gate Innovation and Design Sprinting.
The 5 Whys is one of the root cause analysis tools that can efficiently solve problems by digging deep into the root causes of the problem using the counter-measure method. Its lean nature makes it easy to use and implement during stakeholder meetings. While it proved its efficiency, it can be used alone or with other tools, such as brainstorming to find solutions or a cause-effect diagram to explore the different causes of the problem. It can solve simple and complex issues using a simple methodology, making it more effective than the other root-cause analysis tools.
Summary
The 5 Whys method is a problem-solving technique used to identify the root cause of an issue or problem. It involves asking the question “Why?” multiple times, typically five times, to uncover deeper underlying causes. By repeatedly asking “Why?” and exploring the responses, the method aims to reveal the fundamental cause of a problem rather than addressing only its symptoms.
1- Clearly define the problem: Start by clearly defining the problem you want to address or understand. This problem statement will serve as the starting point for the 5 Whys analysis.
2- Ask “Why?” for the first time: Ask yourself or your team why the problem occurred. Identify the immediate cause or reason that led to the problem. The answer to this question becomes the basis for the next “Why?”.
3- Ask “Why?” for subsequent times: Take the answer from the previous “Why?” and ask “Why?” again. This helps to dig deeper and identify the underlying causes or factors that contributed to the immediate cause. Continue this process for approximately five iterations or until you reach a point where the root cause becomes evident.
4- Analyze the responses: Once you have completed the five iterations of asking “Why?”, review the responses and analyze the patterns or trends that emerge. Look for common themes or underlying causes that appear consistently throughout the questioning process.
5- Identify the root cause: Based on the analysis of the responses, identify the root cause of the problem. The root cause is the underlying factor or issue that, if addressed, can prevent the problem from occurring or recurring.
6- Develop solutions: Once the root cause is identified, brainstorm and develop appropriate solutions or countermeasures to address it. Focus on resolving the root cause rather than just addressing the symptoms of the problem.
Implement and monitor: Implement the selected solutions and monitor their effectiveness. Continuously evaluate and refine the solutions based on feedback and results