What is the Failure Mode and Effects (FMEA)?
Our worst fear in design is to end up with a failed product. At this particular moment, we pause and wonder; if we knew this will going to happen, we could have taken another route. The Failure Modes and Effects Analysis (FMEA) tool help us to understand the potential risks that may occur when the designed product or service is used by the consumers and provide suggested methodologies to prevent it in an early stage of the design process.
Related articles:
Problem-Solving Using Cause and Effect Diagram
Using the TRIZ Method for Creative Problem Solving
Practice Guide to Solve Problems with TRIZ
What is the Failure Mode and Effects Analysis (FMEA)?
The Failure Mode and Effects Analysis provides a proactive method that allows us to evaluate both the design and the process to learn more about when, where, and how the failure may occur. Also, it shows us the failure impact on different parts of the process by prioritizing the risks using three main values; the severity of the risk, its occurrence, and the ability to detect it. Then, the team can apply problem-solving tools such as the SCAMPER technique, TRIZ or 8D Problem Solving Approach.
The Failure Mode and Effects Analysis were first introduced by the U.S. Department of Deference in 1949, and it is now widely used in quality control. It is built on other tools, such as Risk Analysis and the Cause-Effect diagram. It can be used in both the product development process and the business design process.
The Types of the FMEA
The Failure Mode and Effects Analysis can be categorized based on the target part of the production. So, we can categorize the FMEA into the following types:
– Design FMEA explores the product malfunctions that are related to the materials, form, interface component and engineering. These failures may affect factors such as the product life cycle and safety.
– Process FMEA explores the faults related to the production process, including the manufacturing and bringing all the industry components together.
– Functional FMEA explores the faults in how the global system functions
– Service FMEA involves the service design associated with the product
Some added more types to the above list, such as the System FMEA and the Software FMEA. However, the above categories can cover all the possible types of Failure Mode and Effects Analysis.
What are the benefits of the FMEA?
While testing and evaluating the design prototype, several factors can’t be accurately defined unless the product is released and understood from the larger context of user experience, the context of use, technology, economy, and the usage intersection with other products. So, we can benefit from utilising the FMEA risk analysis to:
– Identify and eliminate the risk of potential product problems
– Improve product safety and reliability
– Rescue the cost of the problem fixing in the future product improvement process.
How to Apply the Failure Mode and Effects (FMEA) Process?
The Failure Mode and Effects Analysis is applied in different stages of the product, for example, at the beginning of a new production process, applying changes to an existing product or the production process, applying new production regulations, and of course, to solving a problem reported by the consumer about the product.
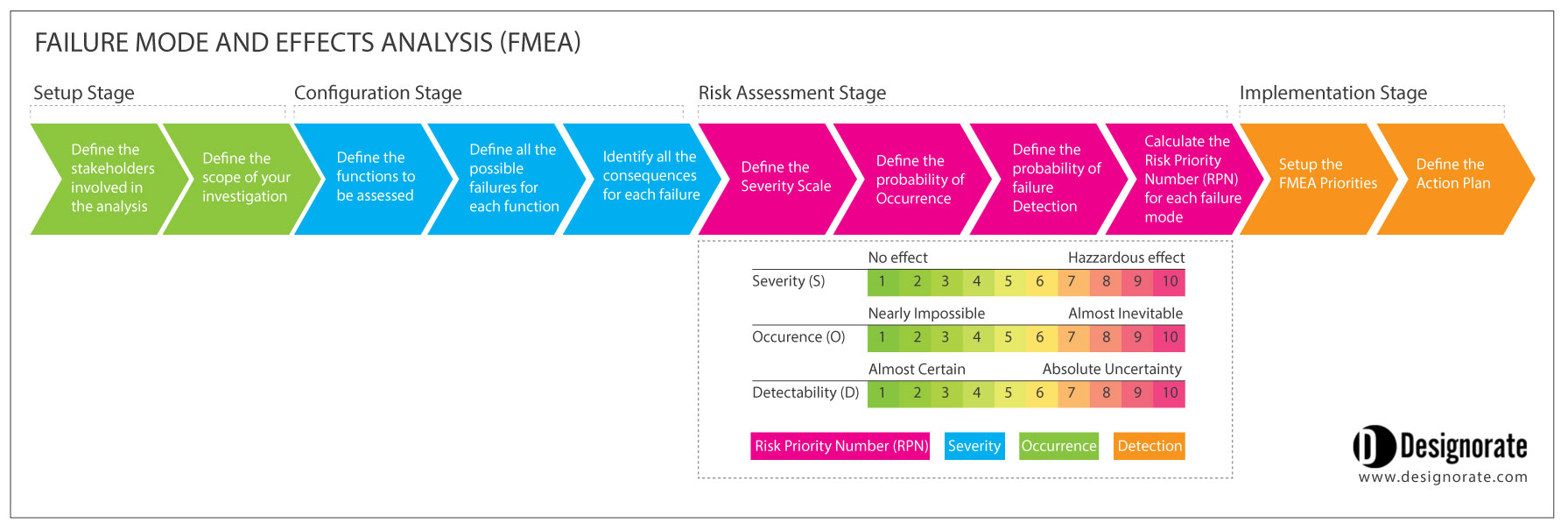
The application of the Failure Mode and Effects Analysis can be made through a number of procedures that are organized in a table as follows:
Setup Stage
This stage starts with defining the stakeholders who will be involved in the Failure Mode and Effects Analysis process. It is crucial that the stakeholders represent the different departments who can advise in relation to the product’s potential risk of failure. Then the team defines the scope of the FMEA process and the scope of the investigation.
Configuration Stage
The aim of this stage is to configure the process by defining the functions of the product that will be assessed and the potential failures that may occur while using the product in relation to each function.
Once the failures were identified, the consequences of each failure were defined before starting to conduct the risk assessment for each failure.
Risk Assessment Stage
In this stage, the FMEA tool is used to determine the risk priority number (RPN) for each failure mode as follows:
1) FMEA Severity Scale
Define the first potential failure that may occur in relation to the product design and process. Each potential failure should be listed individually to avoid distraction and misleading information. In the best example, it is hard to release in time for emergencies that require leaving the car immediately, such as drowning or fire.
Determine the severity level of the fault effect. The standard scale is from 1 to 10, where 1 refers to no effect and 10 means a very example of failure affects the product or system without warning. In our example, the severity level is 10.
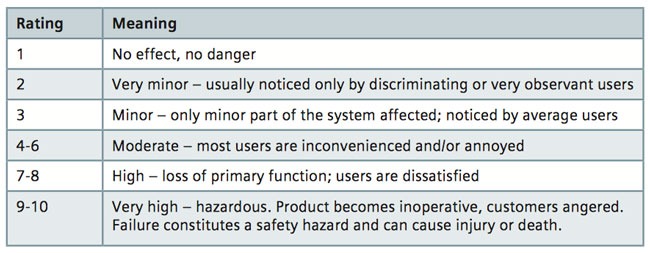
Add the potential cause or causes for the failure. For example, the design of the seat belt lock, the functionality of the lock and how easy to open it when the user intends to do that.
2) FMEA Probability of Occurrence
Add the probability factor, which represents how many times this failure is likely to happen. Again, the common scale is from 1-10, where 1 means that the fault is not likely to happen and 10 means that there is a high probability to occur. In this case, the probability will be 3 as it is assumed that is a lower number of accidents that may occur and requires an immediate release to the seat built.
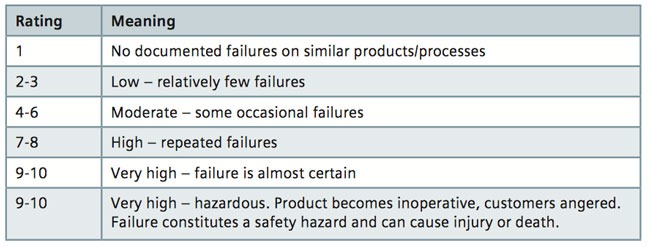
Identify the current procedures that the system is using to prevent such failures from happening, such as testing, monitoring, or applying error-prevention mechanisms. For example, the current lock is designed to be easily released. Its red colour allows the user to easily identify it.
3) FMEA Failure Detection
Determine the detection value for the fault. It represents the likelihood to detect the failure using the current control methods. We use a scale of 1-10 to determine the detection value. However, it is a reversed value compared with the above factors. This means that 1 refers to the error likely to be detected using the current controls and mechanism. The 10 value means that the fault is not likely to be detected. In our example, we will set the detection value to 7 as the testing machine may not involve testing how the drivers release the belt during the time of accidents.
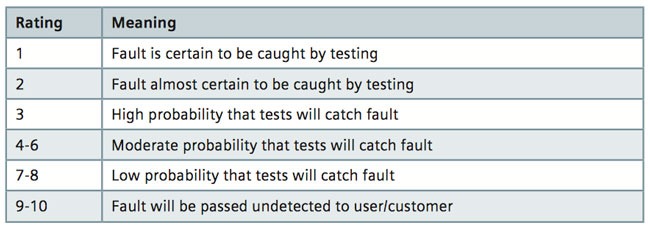
4) Calculate the Risk Priority Number (RPN)
Define the Risk Priority Number (RPN) for failure. The RPN is an equation that includes multiplying the above three factors to prioritize the faults and decide, and understand the importance to solve them. The RPN equation is:
Risk Priority Number (RPN)= Severity x Occurrence x Detection
In our example, the RPN= 10 X 3 X 7= 210

The Implementation Stage
Once the RPN number is calculated for all the potential failures, the team sets up a priority for all the failures and determines the recommended actions that can be applied to prevent these failures in the future. This may involve changing the current controls or improving them to make sure that the detected failure will not occur again in the future. For example, change the position of the lock to make it easier to release during the time of emergencies.
Assign the responsibility of applying the recommended procedures to a person in order to build an action plan to apply these recommendations within the current system structure.
Repeated the above steps with each detected failure. Using the Risk Priority Number, you can determine which fault is more severe than the others and which one to start solving immediately. The table above shows a complete Failure Mode and Effects Analysis that is done to explore solutions for a number of failures in a product. You can use it as a template for future FMEA tasks.
The Failure Mode and Effects Analysis provides a systematic method to detect, analyze and provide a solution for failures that may occur on multiple levels of the production process. It helps the team to indemnify the weak points in the product, process, or system and try to overcome them over the course of improving the production process and, subsequently, the final product or service.
Bibliography:
Carlson, C., 2012. Effective FMEAs: Achieving safe, reliable, and economical products and processes using failure mode and effects analysis (Vol. 1). John Wiley & Sons.
Mikulak, R.J., McDermott, R. and Beauregard, M., 2017. The basics of FMEA. CRC press.
The Failure Mode and Effects Analysis provides a proactive method that allows us to evaluate both the design and the process to learn more about when, where, and how the failure may occur. Also, it shows us the failure impact on different parts of the process by prioritizing the risks using three main values; the severity of the risk, its occurrence, and the ability to detect it.
How to apply The Failure Mode and Effects Analysis?
- Define the product function that has potential failures in the future.
- Define the failures that are associated with the defined function.
- Define the severity scale
Determine the severity level of the fault effect. The standard scale is from 1 to 10, where 1 refers to no effect and 10 means a very example of failure affects the product or system without warning.
- Define the probability of occurrence
Add the probability factor, which represents how many times this failure is likely to happen. Again, the common scale is from 1-10, where 1 means that the fault is not likely to happen and 10 means that there is a high probability to occur.
- Define the failure detection
We use a scale of 1-10 to determine the detection value. However, it is a reversed value compared with the above factors.
- Calculate the Risk Priority Number (RPN)
Define the Risk Priority Number (RPN) for failure. The RPN is an equation that includes multiplying the above three factors to prioritize the faults and decide. The RPN equation is Risk Priority Number (RPN)= Severity x Occurrence x Detection.
- Organise the different failure RPN from high to lower.
- Determine the action plan to improve the product and eliminate potential failures.